روش های تولید فولاد در ایران و جهان
فولادسازی فرآیند تولید فولاد از سنگ آهن و یا قراضه است. در ساخت فولاد، ناخالصیهایی مانند نیتروژن، سیلیسیم، فسفر، گوگرد و کربن اضافی (مهمترین ناخالصی) از آهن اولیه حذف شده و عناصر آلیاژی مانند منگنز، نیکل، کروم، کربن و وانادیوم برای تولید گریدهای مختلف فولاد اضافه میشود. محدود کردن گازهای محلول مانند نیتروژن و اکسیژن و ناخالصیهای درون ریز (که اصطلاحا به آنها “نقص” گفته میشود) برای اطمینان از کیفیت محصولات تولید شده از فولاد مذاب مهم است. طبق آمار انجمن جهانی فولاد و به نقل از وبسایت رسول دانیال زاده نمین، برخی از بزرگترین کشورهای تولید کننده فولاد چین، هند، ژاپن و ایالات متحده هستند. چین تقریباً ۵۰٪ از این تولید را تشکیل می دهد. بزرگترین تولیدکنندگان فولاد جهان شامل ArcelorMittal China Baowu Group Nippon Steel Corporation و HBIS Group هستند.
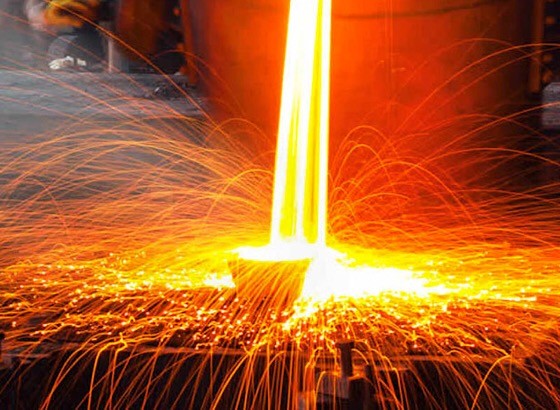
تاریخچه تولید فولاد در جهان
فولاد سازی از هزاران سال پیش وجود داشته است، اما تا اواخر قرن ۱۴ در مقیاس عظیم تجاری نشده بود. یک فرآیند باستانی ساخت فولاد فرآیند تولید فولاد با بوته آهنگری بود. در دهه های ۱۸۵۰ و ۱۸۶۰، فرایند بسمر (Bessemer ) و فرآیند زیمنس-مارتین (Siemens-Martin)، فولادسازی را به یک صنعت سنگین تبدیل کرد. دو فرآیند عمده تجاری برای ساخت فولاد وجود دارد: تولید فولاد به روش اکسیژن قلیایی، که شامل آهن خام مذاب مستخرج از کوره بلند و ضایعات فولاد به عنوان مواد اصلی اولیه است، و فولاد سازی با کوره قوس الکتریکی (EAF)، که از ضایعات فولادی یا آهن احیا شده مستقیم (DRI) به عنوان مواد اولیه تغذیهای استفاده میشود.
تولید فولاد به روش اکسیژن قلیایی عمدتا به دلیل اگزوترمیک طبیعی واکنشهای داخل کوره تأمین میشود. در مقابل، در فولاد سازی EAF، از انرژی الکتریکی برای ذوب قراضه جامد و / یا مواد DRI استفاده می شود. با ورود انرژی شیمیایی بیشتر به فرآیند، فناوری ساخت فولاد EAF نزدیک به فولاد سازی اکسیژن پیشرفت کرده است. در ادامه به بررسی بیشتر هر کدام از این روشهای تولید فولاد پرداخته میشود.
فرآیندهای مدرن تولید فولاد
فرآیندهای مدرن ساخت فولاد را میتوان به دو دسته تقسیم کرد: اولیه و ثانویه. فولادسازی اولیه شامل تبدیل آهن مذاب کوره بلند و ضایعات فولاد به فولاد از طریق فولادسازی به روش اکسیژن قلیایی، یا ذوب آهن قراضه یا آهن احیا شده مستقیم (DRI) در کوره قوس الکتریکی است. فولاد سازی ثانویه شامل تلخیص فولاد خام قبل از ریخته گری است و عملیات مختلف به طور معمول در پاتیلها انجام میشود. در متالورژی ثانویه، مواد آلیاژی اضافه میشوند، گازهای محلول در فولاد کاهش مییابد و مواد حاصل از آن به طور شیمیایی برداشته میشود یا تغییر مییابد تا اطمینان حاصل شود که فولاد با کیفیت بالا پس از ریخته گری تولید شود.
فولاد سازی اولیه
۱- فولاد سازی به روش اکسیژن قلیایی (Basic Oxygen Steelmaking)
فولاد سازی به روش اکسیژن قلیایی روشی از فولاد سازی اولیه است که در آن آهن خام مذاب غنی از کربن به فولاد تبدیل میشود. دمیدن اکسیژن به آهن خام مذاب باعث کاهش محتوای کربن آلیاژ و تبدیل آن به فولاد می گردد. این فرآیند به دلیل ماهیت شیمیایی مواد نسوز – اکسید کلسیم و اکسید منیزیم – که به منظور مقاومت در برابر درجه حرارت بالا و خورندگی فلز مذاب و سرباره، در فرآیند تولید در واکنشها شرکت میکنند، به عنوان اساس تولید فولاد شناخته میشود. ترکیب شیمیایی سرباره نیز کنترل میشود تا اطمینان حاصل شود که ناخالصی هایی مانند سیلیکون و فسفر از فلز خارج میشوند.
این فرآیند در سال ۱۹۴۸ توسط رابرت دورر، با استفاده از خالص سازی کانورتور بسمر که در آن دمیدن هوا با دمیدن اکسیژن جایگزین می شود، توسعه یافت. این روش هزینه سرمایه برای تجهیزات و زمان ذوب را کاهش و بهره وری نیروی کار را افزایش داد. بین سالهای ۱۹۲۰ و ۲۰۰۰، نیاز به نیروی کار در این صنعت با ضریب ۱۰۰۰ کاهش یافت و از بیش از ۳ ساعت در هر تن به ۰٫۰۰۳ ساعت رسید.
اکثریت قریب به اتفاق فولاد تولید شده در جهان با استفاده از کوره به روش اکسیژن قلیایی تولید می شود و در سال ۲۰۱۱ ، ۷۰٪ از تولید جهانی فولاد را به خود اختصاص داده است. کوره های مدرن، شارژ آهن تا ۳۵۰ تن را در خود دارند و آن را در کمتر از ۴۰ دقیقه در مقایسه با ۱۰-۱۲ ساعت کوره آتشدان روباز به فولاد تبدیل میکنند.
شارژ فلز داغ به کوره BOS
در این روش تولید فولاد یک مقدار جزئی اکسیژن خنک شده با آب به درون کانورتور پایین آمده و اکسیژن با خلوص بالا با فشار بسیار بالا به فلز منتقل میشود. اکسیژن با کربن و سایر عناصر ناخواسته ترکیب می شود و آنها را از بار ذوب خارج میکند. این واکنش های اکسیداسیون گرما تولید می کنند و دمای فلز توسط مقدار قراضه اضافه شده کنترل می شود.
کربن از کنورتور به عنوان یک گاز یعنی مونوکسیدکربن خارج می شود که می تواند برای استفاده مجدد به عنوان سوخت جمع شود. در طول دمش ، آهک به عنوان شارژ اضافه می شود تا به کمک آن سایر ناخالصیهای اکسید شده به عنوان یک لایه شناور از سرباره جدا شود. مقادیر قراضه، فلز داغ و آهک و سایر شارژها برای اطمینان از درجه حرارت و ترکیب درست فولاد محاسبه می شوند.
در بسیاری از کارخانهجات، فرآیند تخلیص با دمش گازها، از جمله آرگون، نیتروژن و دی اکسید کربن از انتهای کوره انجام میشود. بعد از اینکه فولاد تلخیص شد و از نمونه ها برای بررسی دما و ترکیب آن استفاده شد، کنورتور کج شده و فولاد به پاتیل ریخته میشود. به طور معمول، میزان کربن فولاد در پایان تلخیص حدود ۰۴/۰٪ است. در حین ریختن به پاتیل، میتوان برای تنظیم ترکیب نهایی فولاد، از افزودنیهای آلیاژی استفاده کرد.
۲- فولادسازی با کوره قوس الکتریکی (Electric Arc Furnace)
فولاد سازی کوره قوس الکتریکی ساخت فولاد از قراضه یا آهن احیا شده مستقیم است که توسط قوسهای الکتریکی ذوب می شود. در یک کوره قوس الکتریکی، ممکن است دسته ای از فولاد (گرم) با بارگذاری قراضه یا آهن احیا شده مستقیم به داخل کوره، گاهی اوقات با مانده ذوب (فولاد مذاب از گرمای قبلی)، شروع شود. مشعل های گازی ممکن است برای کمک به ذوب شدن توده قراضه در کوره استفاده شوند.
در این روش همچون ساخت فولاد به روش اکسیژن قلیایی، شارژهایی نیز برای محافظت از پوشش مخزن و کمک به بهبود حذف ناخالصیها اضافه میشوند. در ساخت فولاد با کوره قوس الکتریکی معمولاً از کوره هایی با ظرفیت حدود ۱۰۰ تن استفاده می شود که برای پردازش بیشتر هر ۴۰ تا ۵۰ دقیقه فولاد تولید میکنند.
این فرآیند در اصل فقط برای ساخت فولاد با کیفیت بالا، مانند مواردی که برای ماشین آلات و فولاد فنر استفاده می شود، مورد استفاده قرار میگیرد، زیرا کنترل دقیقتری بر ترکیب شیمیایی فولاد تولید شده میتوان داشت. امروزه، این روش همچنین در ساخت فولادهای پرکاربرد از جمله گریدهای آلیاژی و ضد زنگ و همچنین برخی از فولادهای خاص کربنی و کم آلیاژ استفاده میشود. کوره های قوس الکتریکی مدرن می توانند در یک ذوب تا ۱۵۰ تن فولاد تولید کنند.
کوره قوس الکتریکی شامل یک حمام دایرهای شکل با سقف متحرک است که از طریق آن می توان سه الکترود گرافیتی را در جهت بالا و پایین حرکت داد. در آغاز فرآیند، الکترودها خارج شده و پس از آن ضایعات فولادی از یک سبد بزرگ فولادی توسط یک جرثقیل سقفی به کوره شارژ میشود. هنگامی که شارژ کامل شد، سقف دوباره به موقعیت خود برگردانده شده و الکترودها در پایین کوره قرار میگیرند.
یک جریان الکتریکی قوی روی شارژ اضافه شده اعمال میشود، یک قوس ایجاد شده و گرمای تولید شده ضایعات را ذوب میکند. آهک و فلورسپار به عنوان شار اضافه میشوند و اکسیژن در مذاب دمیده می شود. در نتیجه، ناخالصی های موجود در فلز با هم ترکیب می شوند و یک سرباره یه حالت مایع را تشکیل میدهند.
نمونه هایی از فولاد گرفته شده و برای بررسی ترکیب آنها تجزیه و تحلیل می شود و هنگامی که ترکیب و درجه حرارت مناسب و درست بدست آمد، محتویات کوره به سرعت به پاتیل منتقل میشود. تنظیمات نهایی برای مشخصات دقیق مشتری را می توان با افزودن آلیاژها در حین انتقال یا متعاقباً در یک واحد ساخت فولاد ثانویه انجام داد.
فولاد سازی ثانویه
بعد از اینکه فلز مذاب از کوره BOS یا EAF به پاتیل منتقل شد، بسته به گرید فولاد مورد نیاز، اغلب یک یا چند عملیات اضافی انجام میشود. این مراحل تلخیص اضافه شده به فرآیند در مجموع به عنوان فولاد سازی ثانویه شناخته میشوند و می تواند شامل اکسید زدایی (یا اصطلاحا اکسیژن کشی)، هم زدن پاتیل با آرگون، تزریق پودر یا سیم، گاززدایی در خلا و گرم شدن قوس پاتیل باشد. در تولید فولادهای گرید بالا همه این عملیات را با هم ترکیب میکنند. این فرایندها همگن سازی دما و ترکیب را بهبود می بخشد، باعث میشوندکه ترکیب دقیقتری حاصل شده، گازهای مضر و ناخواسته مانند هیدروژن از بین برود و عناصری مانند گوگرد را به مقادیر بسیار پایین کاهش دهد.
فولاد سازی HIsarna
در فرآیند ساخت آهن HIsarna، سنگ آهن تقریباً مستقیماً تبدیل به آهن مذاب یا فلز داغ می شود. این فرآیند بر پایه نوعی کوره بلند به نام کوره کانورتور سیکلون استوار است و این امکان را می دهد که فرایند تولید ساچمه های آهن خام را که برای فرآیند تولید فولاد به روش اکسیژن قلیایی لازم است، کنار گذاشته شود. بدون نیاز به این مرحله مقدماتی ، فرآیند HIsarna از نظر انرژی صرفه جویی بیشتری دارد و میزان انتشار کربن کمتری نسبت به فرآیندهای سنتی ساخت فولاد دارد.
محصولات جانبی تولید فولاد
مانند تمام فرآیندهای تولید در مقیاس بزرگ، تولید آهن و فولاد محصولات جانبی مخصوص خود را دارند. به طور متوسط تولید ۱ تن فولاد منجر به تولید ۲۰۰ کیلوگرم (EAF) تا ۴۰۰ کیلوگرم (BF / BOF) محصولات جانبی می شود. محصولات جانبی اصلی تولید شده در طول تولید آهن و فولاد خام، سرباره (۹۰٪) ، گرد و غبار و لجن (sludges) است. متوسط نرخ بازیابی سرباره در جهان از بیش از ۸۰٪ برای سرباره فولاد سازی تا تقریبا ۱۰۰٪ برای سرباره آهن سازی متفاوت است. سه نوع اصلی تولید آهن یا سرباره BF در بازار وجود دارد که بر اساس نحوه خنک سازی دسته بندی می شوند – هوا خنک ، دانه بندی و گلوله (یا منبسط).
سرباره هوا خنک، سخت و متراکم است و مخصوصاً برای استفاده به عنوان مصالح ساختمانی مناسب است. این ماده همچنین در بتن آماده، محصولات بتونی، بتن آسفالتی، مواد پر کننده ، مواد اولیه کلینکر، پشم معدنی (برای استفاده به عنوان عایق) و نرم کننده خاک استفاده می شود.
سرباره گرانول ذرات شیشه ای به اندازه ماسه را تشکیل می دهد و در درجه اول برای ساخت مواد سیمانی استفاده می شود. سرباره پلت شده یا منبسط دارای بافت تاولی شکل (مانند سنگ آتشفشانی) است و معمولاً به عنوان یک سنگدانه سبک استفاده می شود. اگر ریز خرد شود، خواص سیمانی نیز دارد. سرباره فولاد سازی (BOF و EAF) به طور مشابه سرباره BF با هوا خنک می شود و برای بیشتر اهداف مشابه استفاده می شود. از آنجا که فرآیند تولید در این مرحله بسته به نوع فولاد ساخته شده متفاوت است، سرباره های بدست آمده نیز دارای خواص شیمیایی متنوعی هستند که استفاده از آنها را نسبت به سرباره های آهن ساز دشوارتر میکند
تولید فولاد در ایران
تولید فولاد در ایران به طور معمول با دو روش زیر انجام میشود. در روش اول که در ذوب آهن اصفهان اتفاق میافتد، فولاد در کورههای احیای اکسیژن با مذاب آهن خام حاصل از کوره بلند تولید میشود. بدین صورت که باید سنگ آهن به همراه آهک و کک وارد کوره بلند شده و آهن خام تولید می شود و در مرحله بعد این آهن خام به فولاد مذاب تبدیل میگردد و پس از جداسازی ناخالصیهای آن فولاد خام تولید میشود. در روش دوم نیز که در فولاد خوزستان و مجتمع فولاد جنوب است، فولاد خوزستان، تولید انواع شمش فولادی میپردازد.
فولاد سازی با کوره های قوس الکتریکی و القایی انجام میشود. در این روش که شامل احیای مستقیم آهن است، از قراضه آهن و یا آهن اسفنجی استفاده میشود. به دلیل کمبود قراضه آهن در ایران در این روش بیشتر از آهن اسفنجی بهره گرفته میشود و متعاقبا درصد بالایی از فولاد خام توسط آهن اسفنجی تولید میشود. بیشتر فولاد خام جهان از روش اول و به وسیله کورههای بلند تولید میشود ولی تولید فولاد با روش دوم توجیه پذیرتر خواهد بود.
تولید فولاد در کوره های الکتریکی به دلیل استفاده از قراضه آهن سریع تر بوده و همچنین هزینه ایجاد یک کوره بلند بسیار بیشتر از ایجاد کورههای الکتریکی است. علاوه بر آن روش کوره بلند محدودیت زیست محیطی بیشتری نسبت به روش احیای مستقیم دارد و همچنین آهن اسفنجی دارای عیار بالاتری است و حمل و ذخیره آن نیز آسان تر میباشد.